Melbourne Water Contract
Customer:
Through the 80s and 90s, parallel to the Gas & Fuel contract, we also had an annual supply contract with Melbourne Water to supply 20mm Class 2 Crushed Rock, 20mm Class 3 Crushed Rock, Bedding Sand, and topsoil to their Melbourne depots, such as Mitcham, Moorabbin, and Dandenong depots.
At a later stage, Thiess Contractors was awarded the contract to do all the works for Melbourne Water. After experiencing our service and reliability over the years, Melbourne Water recommended us to Thiess, and we continued supplying materials for the remaining works.
Over three stages, we delivered nearly 80,000 tonnes, maintaining strict quality standards and keeping the project ahead of schedule, cementing our reputation as a trusted partner.
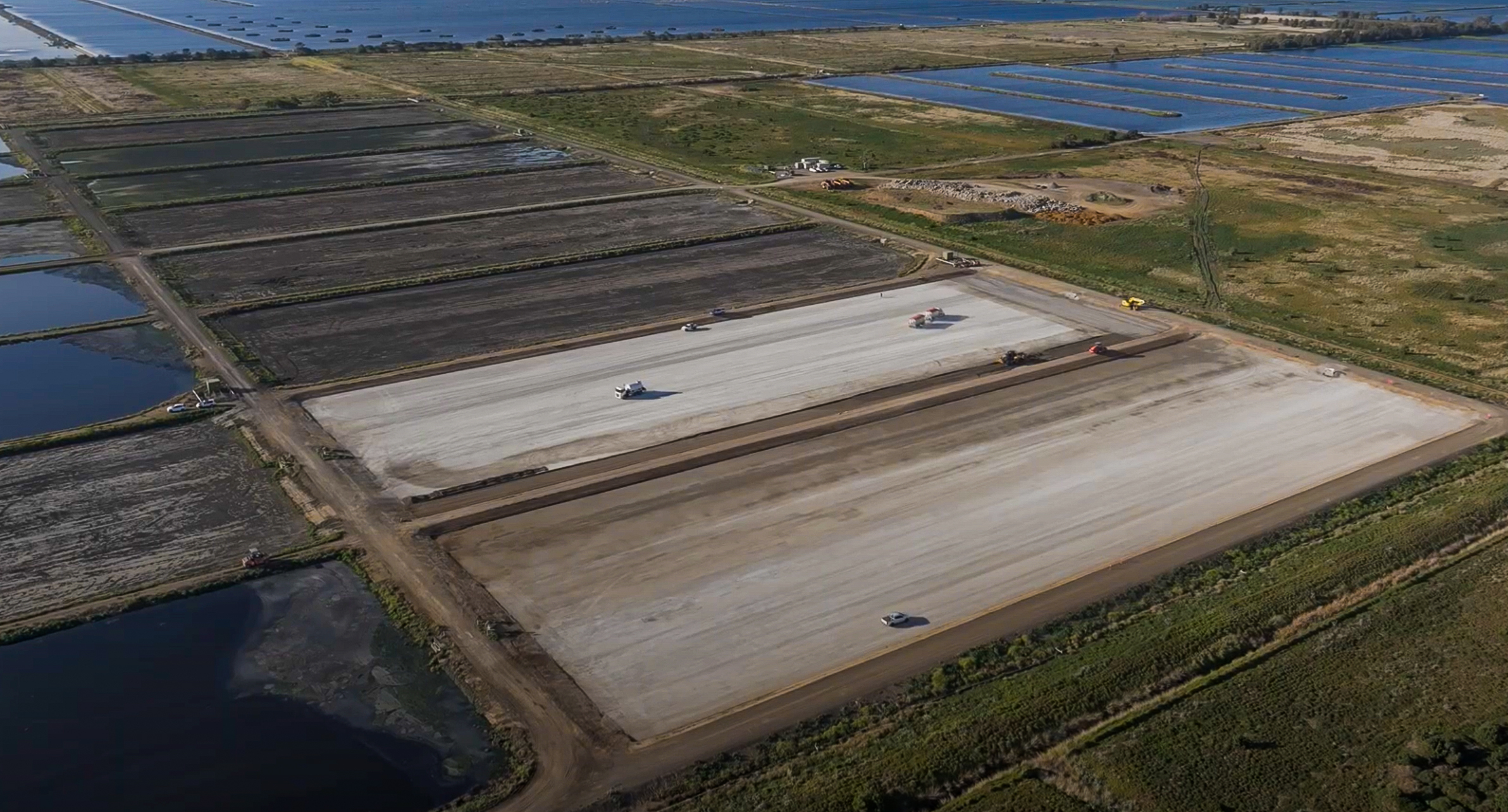
The Challenge
At the time, the construction industry was grappling with high material demand, driver shortages, and supply chain pressures. Quarries faced frequent breakdowns and stock shortages, and drivers were in high demand, making it challenging to guarantee large volumes of material. These risks called for a partner with extensive networks, deft processes, and the ability to call upon contingency suppliers or drivers in the event of breakdowns or delays.
A long-term customer recommended Lofts to Melbourne Water due to our proven track record of reliability, care, and quality service. Having successfully supported multiple large projects for them, they had experienced our personalised approach and ability to leverage a robust network of suppliers and drivers and keep projects moving, even when there is limited supply available. Melbourne Water entrusted us with pans 1 and 2 and then awarded us another two stages based on the service and reliability they had experienced.
The Challenge
At the time, the construction industry was grappling with high material demand, driver shortages, and supply chain pressures. Quarries faced frequent breakdowns and stock shortages, and drivers were in high demand, making it challenging to guarantee large volumes of material. These risks called for a partner with extensive networks, deft processes, and the ability to call upon contingency suppliers or drivers in the event of breakdowns or delays.
A long-term customer recommended Lofts to Melbourne Water due to our proven track record of reliability, care, and quality service. Having successfully supported multiple large projects for them, they had experienced our personalised approach and ability to leverage a robust network of suppliers and drivers and keep projects moving, even when there is limited supply available. Melbourne Water entrusted us with pans 1 and 2 and then awarded us another two stages based on the service and reliability they had experienced.
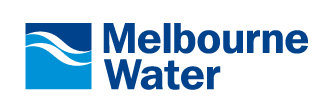
Our Approach and Solutions
- Extensive Supply Network and ContingenciesLofts leveraged its vast network of material suppliers and transport providers to ensure uninterrupted deliveries. By avoiding sole reliance on a single source of drivers and materials, we minimised risks associated with supply chain disruptions and could guarantee continuous supply.
- Responsive, Flexible DeliveriesInitially contracted to deliver 800 tonnes per day, Lofts adapted to Melbourne Water’s evolving needs, increasing deliveries to 1,700–1,800 tonnes daily and even reaching peaks of 2,000 tonnes. Despite unplanned challenges, such as adverse weather, Lofts maintained flexibility, scaling deliveries up or down as required. This adaptability not only met the schedule but often accelerated it, reducing overall project timelines.
- Quality AssuranceThe project required VicRoads-approved 20mm Class 3, 3% CTCC, demanding strict adherence to moisture and composition standards. Each batch was rigorously tested, and results were promptly reported to Melbourne Water. This ensured every load met specifications, reducing the risk of delays from rework or material inconsistencies.
- Proactive CommunicationLofts maintained transparent, proactive communication throughout the project. Directors and a dedicated operations team oversaw progress, provided regular updates, and responded swiftly to changes. This seamless coordination allowed the team to adapt to unforeseen circumstances while maintaining project continuity.
- Senior Oversight and DedicationSenior management remained deeply involved from start to finish, aligning operations with Melbourne Water’s unique requirements. Post-project assessments further reinforced our commitment to quality, reliability, and continuous improvement—a standard we’ve upheld since 1979.

Key outcomes
- Project Efficiency:
- Stage 1 (Pans 1 & 2): Planned 6.5 weeks; completed in ~4 weeks
- Stage 2 (Pans 3 & 4): Planned 6.5 weeks; completed in ~3 weeks
- Stage 3 (Pans 23 & 24): Planned 6.5 weeks; completed in ~5.5 weeks (deliveries put on hold, solely due to site requirements and weather)
- Volume Delivered:
Across three stages, Lofts delivered nearly 80,000 tonnes of VicRoads-approved 20mm Class 3, 3% CTCC and doubled the expected daily delivery volumes.
- Reporting and Compliance Excellence:
- Exceeding Expectations:
We would like to extend a big thank you to Melbourne Water for the opportunity to supply this project and to Boral & Delta Group for their reliable material supply and technical support.
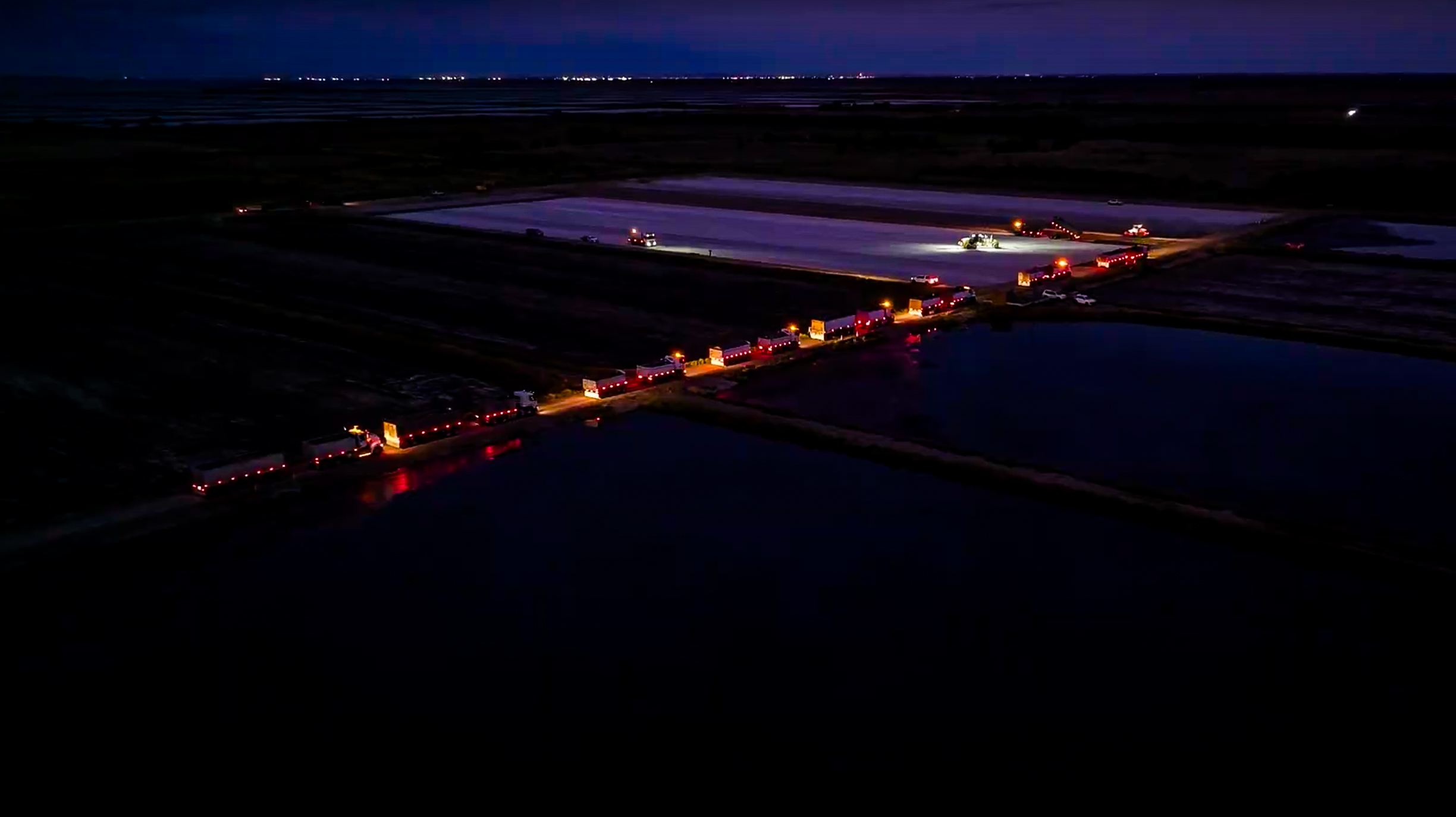
Conclusion
Why Lofts?
For over 45 years, Lofts has combined the capability to handle large-scale projects with the personalised service of a small business. Our extensive network, customer-centric approach, and unwavering commitment to quality make us the partner of choice for critical infrastructure projects.
The success of the Western Treatment Plant renewal underscores Lofts’ ability to provide reliability, adaptability, and excellence—delivering results that build confidence and drive progress.